Installer 17 mixeurs de plus de vingt tonnes chacun dans BBD2, comment ça marche ?
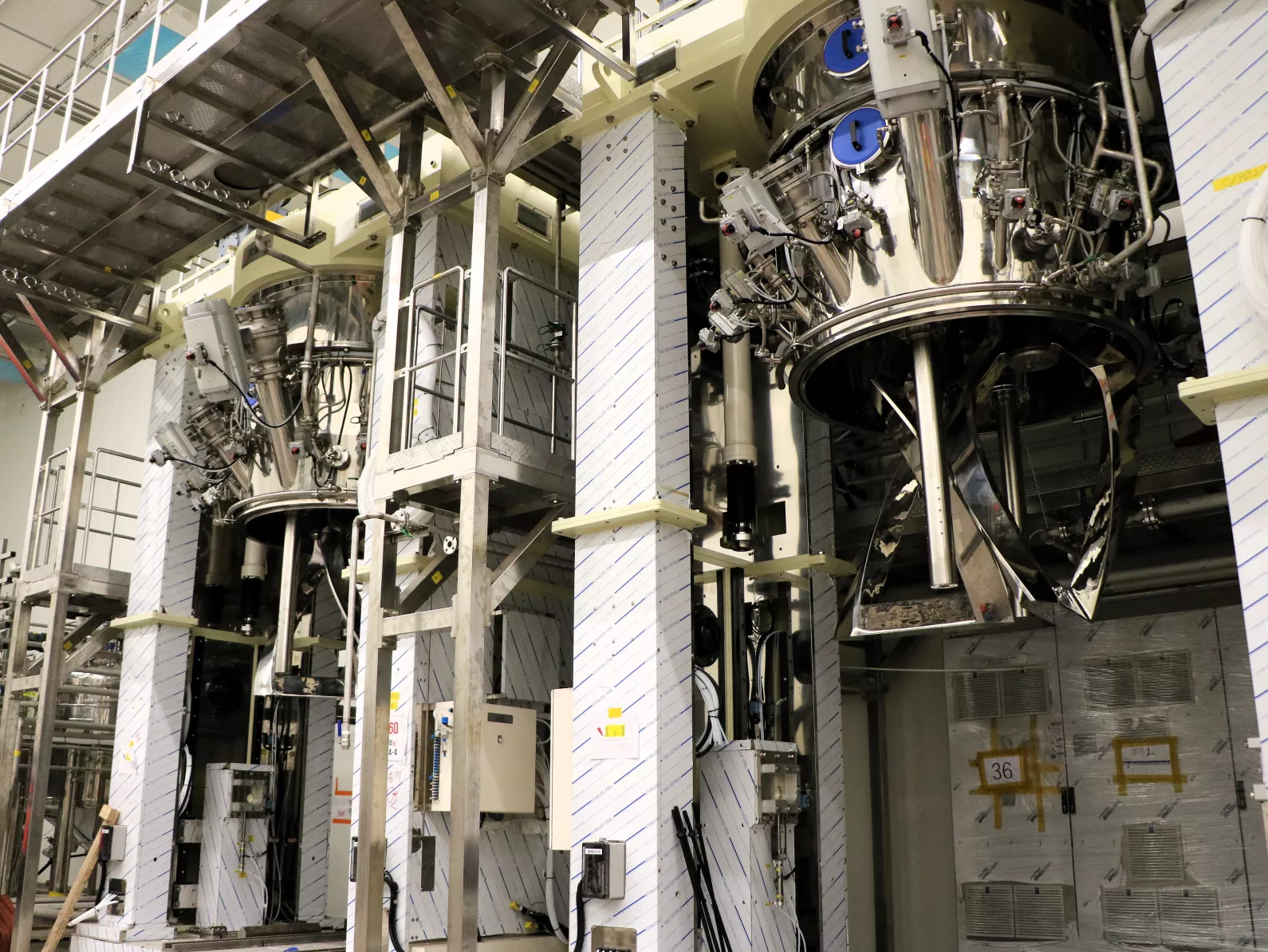
Vingt mois après le démarrage du chantier de construction du deuxième bloc de la Gigafactory ACC de Billy-Berclau Douvrin, l'heure est à l'introduction des machines de production, qui aboutira à un démarrage envisagé en octobre 2025.
Après les fours de séchage au coating, qui ont été installé sur une immense structure porteuse, restons dans le secteur de la chimie pour d’autres installations de taille : les PD Mixers, pour « Planetary disperser mixers ». De quoi s’agit-il ?
« Un PD mixer, c'est le mélangeur principal dans la fabrication des électrodes, c'est là où on vient ajouter les matériaux conducteurs, toutes les poudres qui sont utilisées pour produire une électrode de batterie, avec des solvants, pour fabriquer une encre qui va ensuite être enduite et suivre le procédé de production de batterie », explique Marcos Oliveira, ingénieur process au Mixing de BBD2.
Chaque PD Mixer a une capacité de 1200 ou 1600 litres. Dix-sept de ces engins hors normes seront installés dans cinq salles de Mixing.
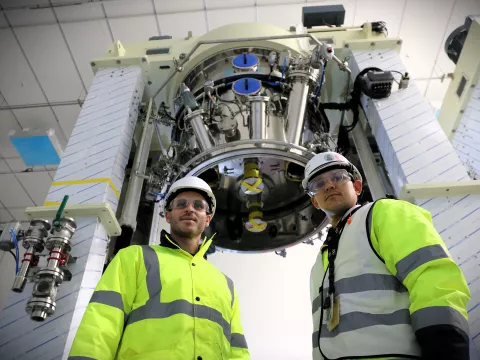
Leur installation n’a rien d’une formalité, puisque les mixeurs sont positionnés dans les futures salles sèches cloisonnées.
Rendez-vous dans une des deux salles côté cathode, où trône une installation inhabituelle. « Suite au marquage au sol pour les positionnements des équipements, on vient installer un portique hydraulique avec la capacité de lever des équipements à plusieurs tonnes. Ici, on a des machines qui vont aller au-delà des 20 tonnes par partie de PD Mixer. Donc on utilise ça pour positionner au centimètre près les parties du PD mixer qui doivent être assemblées en salle », décrit Marcos Oliveira.
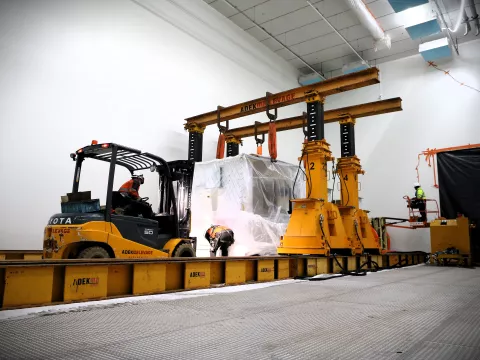
Le PD mixer est tellement encombrant qu’il est transporté en camion et introduit dans le bâtiment en deux parties distinctes, plus les moteurs d’agitation, assemblés sur la partie haute dans la salle de Mixing, d’une superficie de 450 m2, avec une hauteur sous plafond de dix mètres. « On vient placer la partie basse et ensuite on lève cette partie haute avec les moteurs d'agitation, qui pèse plus de 20 tonnes », détaille Marcos Oliveira.
Les délais d’exécution sont extrêmement réduits, en raison de l’expertise des équipes à la manœuvre. « En une semaine, on arrive à installer le portique hydraulique et à poser quatre PD Mixers. En deuxième semaine, on place les plateformes qui vont jusqu’à 7 mètres et nous permettent d’avoir accès aux différents niveaux du PD Mixer. Ensuite on va rentrer des sous-mixeurs qui permettent de produire d’autres composantes de l’encre, qui vont aller dans le mélange global dans le PD Mixer. »
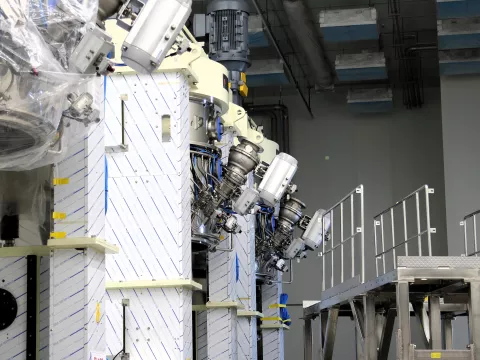
Ce n’est pas tout, poursuit Marcos : « Il faut compter environ quatre semaines pour poser les équipements dans une salle. Ensuite il y aura des travaux de tuyauterie, toute la partie électrique. Ca fait un total entre 12 et 16 semaines entre l’installation du portique jusqu’au raccordement électrique des machines. Et après on fait les premiers tests de mise en service, puis la production. »
Les deux autres salles seront équipées cet été, et Marcos sera encore là pour superviser cette opération. Avant d’arriver chez ACC, en septembre 2024, il travaillait dans le traitement de l’eau, à Paris. A son arrivée, la dalle de béton dans la zone de Mixing n’était pas encore posée. Six mois plus tard, huit PD Mixers ont été installés. De quoi donner le sourire à Marcos, pour qui le projet ACC est « magique » : « Avoir la gestion de ces interfaces lors de l'installation, ça permet vraiment de connaître le détail de la machine, comment on l'a raccordée, comment elle fonctionne, comment elle réagit en production, tous les circuits… »
Car Marcos se projette déjà vers la mise en service, programmée à la fin de l’année. Avec une casque d’ingénieur process sur la tête, à ce moment-là.
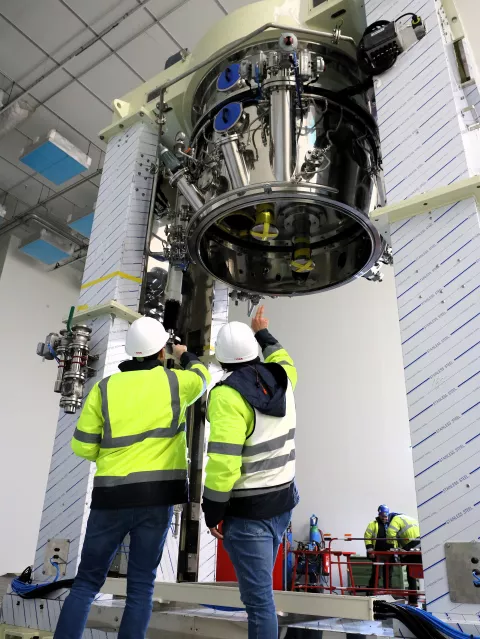