Catching up on e-mobility - Rheinpfalz
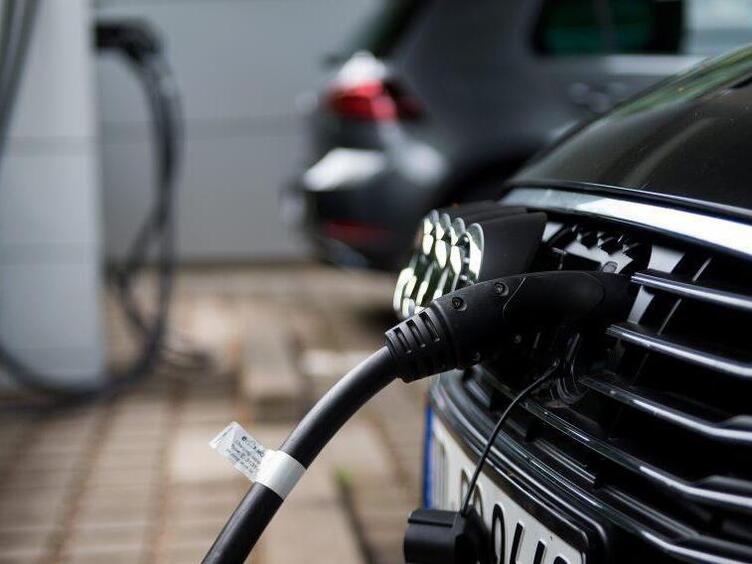
In autumn, part of the Opel halls will be demolished, and in 2025 the first products are to be produced on the site: this is the plan of the battery cell manufacturer ACC (Automotive Cells Company). The aim is to make Europe independent of Asia in e-mobility.
BY GUNDULA ZILM https://www.rheinpfalz.de/
Anyone who thinks of young computer nerds in children's rooms or their parents' garage when they hear the term start-up will get a different picture at ACC. The number of employees – a full eleven – may still be in the cool, as well as the used chairs or improvisation in the absence of a glass of water. But all the other figures make it clear that something very big is emerging in Kaiserslautern: ACC has a total investment volume of seven billion euros, the German plant alone will receive 436 million euros in funding from the federal and state governments and is expected to offer around 2000 jobs in 2030, explains Peter Winternheimer, who is setting up and managing the German site as Vice President. After more than 26 years in the service of Opel, including almost eleven years as head of the Lauterer plant, then in the parent company Stellantis, he "seized the opportunity to participate first-hand in the transformation of the automotive industry – you only get it once in a lifetime," he is convinced. With the production of car battery cells, Kaiserslautern will become a centre fore-mobility in Europe, "and we will not be able to produce as much as demand will demand". The "founders" have still only rented one corridor from Opel, but by 2030 there are to be three production lines at this location, of which the first two alone with the dimensions of 650 by 200 meters are to be circumnavigated "already a small jogging round", peter Hamel describes it, responsible for communication at ACC.
Depending on China
The history of ACC began in August 2021 with a competence centre in Bordeaux, and since then a test factory has been built in Angouleme, which is located next to it. "Currently, 85 percent of all car batteries come from Asia." In order to free itself from this dependency, ACC wants to set up a battery cell production facility in Europe. The first plant is scheduled to go into operation next year in northern France, the second in Kaiserslautern in 2025 and the third in central Italy in 2026. For this step, however, ACC first needs help from China and South Korea, where the machines for battery cell production are built. "We have no option, there are no European or German suppliers," says Winternheimer – without saying that Germany has overslept the development of e-mobility. And when asked, he pushes back: "We still don't have to rethink our business relationships because of the current development."
The machines will then be used to manufacture the battery cells for local needs. It is obvious that Stellantis and Mercedes will be customers, because together with the TotalEnergies subsidiary Saft – a battery manufacturer – they are each one third shareholders of ACC. "Stellantis itself lacks the expertise for battery production," Winternheimer explains why the Group does not take over this itself. "Automotive manufacturing is metal industry, battery manufacturing chemical industry." ACC itself does not want to build production machines, but rather a European supplier pool. "This will develop in the currently extremely growing market for battery manufacturers in Europe," says Hamel.
Batteries for 500,000 cars
From October or November, the first, already empty Opel hall in Kaiserslautern will be demolished, and construction of the first ACC block will begin in April or May. "From the end of 2025, we will have a production capacity of 13.4 gigawatt hours per year," Winternheimer predicts. Directly adjacent to the first, the second elongated production block is built. With the third block on ACC wants to achieve a production capacity of the 41-hectare area "of 40 gigawatt hours by 2030, so that around 500,000 to 800,000 vehicles can be equipped with batteries".
But the halls and machines alone do not build battery cells. "We will start production with around 650 jobs", some of which will be taken over by Stellantis, and in 2030 there will be around 2000. For this, "highly qualified personnel are needed, specialist workers,"Winternheimer announced. The acquisition of engineers for planning and development is already underway. The production of the battery cells, which is supposed to run around the clock, "does not look like rocket-technology," admits the boss with such a specimen in his hand, but requires an absolutely clean and dry environment.
The many copper and aluminium foils are machine-layered and underlaid with release foils; If a dust gets in between, it could grind the release film and cause a short circuit. "The employees in the dry cleaners with a maximum humidity of one percent must therefore work with a full-bodysuit." How they get to drink and their breaks without losing too much time to change clothes, "we are currently working on models for this".