First very conclusive test on coating
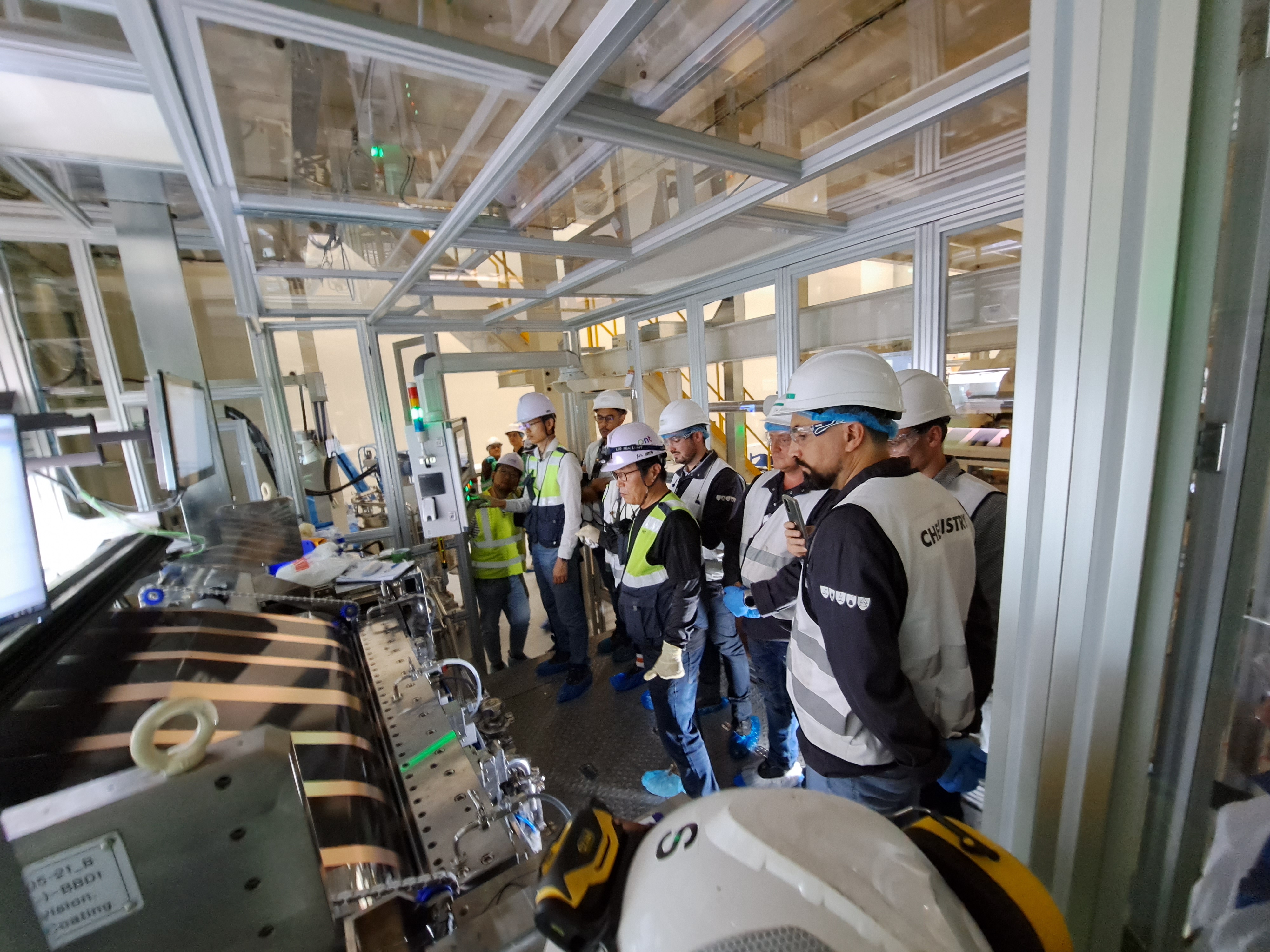
In the space of just two weeks, the Chemicals sector of the Billy-Berclau Gigafactory has achieved two major milestones in the start-up of its production process. On July 20, the team produced its very first ink locally, on the anode side. This mixture of mixed raw materials takes the form of a black liquid paste.
To form an electrode, this ink has to be coated onto a strip of copper on the anode side (negative polarity) or aluminum on the cathode side (positive polarity).
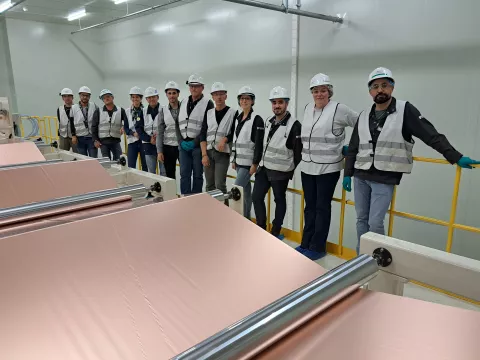
This very thin foil is loaded into rolls on a machine, and runs through a complex process until the ink strips are applied. The coated strip continues its journey through drying ovens. It is coated on its second side in another coating room, and returns to its starting point through a second row of ovens, located on the coating line floor.
The first coating tests were completed in two days. On Wednesday July 26, all parameters were validated to launch the first coating.
Meticulous checks on oven temperature and strip running speed, for example, enabled the very first coating in the history of the Billy-Berclau Gigafactory to get underway at precisely 3:22 p.m., in the presence of calm, well-prepared and focused teams.
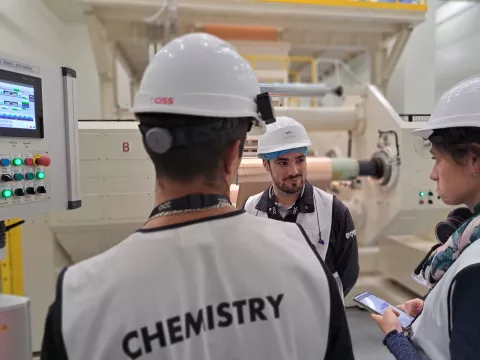
They methodically applied their standards. Less than two minutes later, the first coated and dried strips appeared. They were thoroughly examined by a Quality team. Numerous checkpoints revealed that the coated strips complied with specifications.
Next up for the Chemistry team: continuous coating of both sides of a strip, at higher speeds, and delivery of the "coated" foils for calendering, a step which involves pressing the strips between rollers.
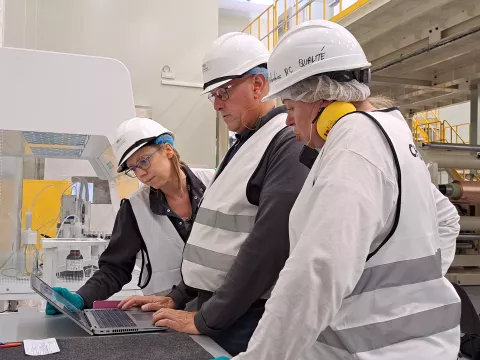