ACC plays the multimodal card to accelerate the decarbonisation of transport
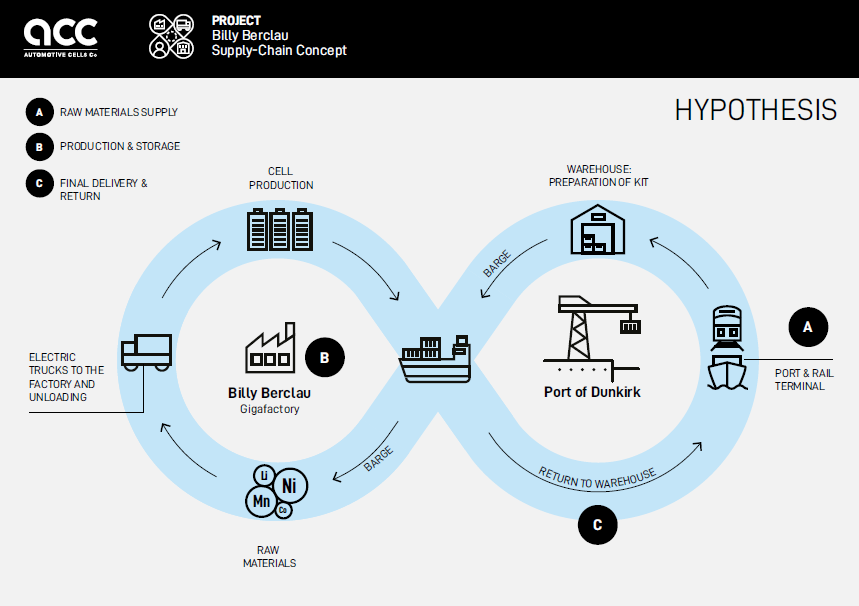
Now that we’ve calculated our carbon footprint and we have identified the impact of our production on the environment, we are actively working at reducing it as much as we can, starting with our supply chain.
Christophe Eglizeaud is a Supply Chain Engineer at ACC. He might be getting a few grey hairs, but Christophe never stopped playing with trains and boats. His job? Finding the most optimal route and the best means of transport for our products and raw materials, in order to reduce costs, lead times, and the carbon footprint of our gigafactories’ supply chain. In other words, Christophe is responsible for the economic and ecologic performance of our supply chain. With a few constraints: the factories are working on a ‘just-in-time’ basis. Cells and raw materials can’t be stored for long, due to reasons of space and performance. Every day, the factory needs to receive the necessary materials for production and send out the results of that production. Additionally, the solution needs to be scalable as our production will ramp up until 2030.
Taking stock of our supply chain needs and specificities
Christophe first looked at the geographical positioning of our factories: Located in the Hauts-de-France, Billy-Berclau Douvrin is easily accessible from the North Sea. The area on which the factory is being built is served by roads, but these are very congested already so adding trucks was not an option. On top of it, trucks can only circulate on weekdays; Sundays and bank holidays, traffic is limited. Since we will be producing around the clock, we needed a solution that would work every day. An old trainline also served the site – back in the day it was used by the Française de Mécanique to convey materials, but it was shutdown in 2000. The cost of refurbishing was prohibitive – close to 10 million euros, so not an option either.
However, a canal is serving the industrial zone. We could build a quay on the public domain, that would mainly be used by us, and chartering electric barges from this quay to the port of Dunkirk. There, a large warehouse could be built to receive and store supplies and raw materials coming from Asia and elsewhere by sea, and products due to be shipped to our clients. That sounded promising.
That’s how we came to design a multimodal transport strategy.
What is multimodal transportation?
Multimodal transportation combines several different modes of transportation to get deliveries from one place to the other. Rather than depend on one means of transport, multimodal shipping uses two or more, thus exploiting the benefits of each mode of transport for better efficiency and flexibility. Using this method, logistic managers can reduce transport costs, inventories and the carbon footprint of the shipment, while optimizing lead times.
Identifying scenarios and phases
Our first point of focus is obviously Billy-Berclau Douvrin. At the start, the production will be limited. A small warehouse close to the Gigafactory with barge connection will suffice. But once our three gigafactories will be in full production phase, we will need to focus on our capacity to supply our three giga plants, by barge, truck and/or rail connections. Multi-warehouse solutions are thus being explored.
Christophe is working alongside several shippers and consultants to draw scenarios and analyze data and locations to find the most efficient mode of transport according to its constraints. How many containers can we put in a trailer, on a train or in a barge? What weight and volume can be accommodated? How many shipments can be ensured every day, etc.
Distances are being analyzed to and from our strategic locations. All inbound and outbound trips are calculated, and scenarios are being compared.
From there, they recommend the best locations, estimated the volumes, the costs, equipment, and resources needed, and the best organization to be undertaken for the implementation.
Our most probable scenarios is as such:
The factory expresses its need. Raw materials from Europe or Asia are being delivered by boat in Dunkirk, kits are being prepared in the warehouse, a barge is being loaded with the orders and materials are being delivered by barge within 8 hours of the order if there are no delays at the locks. Small trucks, with or without drivers complete the last mile to the factory.
Once the barges have unloaded their supplies in Billy-Berclau Douvrin, they collect the cells produced in the factory and return to Dunkirk, where the cells can be sent by train to European customers.
It’s the same scenario for Kaiserslautern. Lauterbourg, at the tip of Alsace, will likely be our port of registery. There too, we are moving towards the creation of a warehouse which would receive the products from our suppliers or from Dunkirk, via the Antwerp canal. Then, as above, kit will be delivered, and production will be sent daily.
Termoli will differ slightly since the factory is close to the sea. Studies are still being undertaken to define the best scenario.
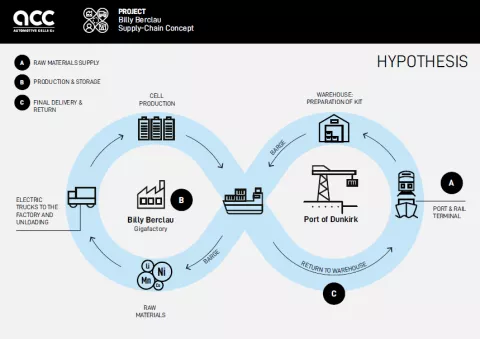
Optimizing our routes to reduce our carbon footprint and optimize cost efficiency
Now imagine: an electric barge can contain 60 to 80 containers. What if we had to convey these 80 containers by truck? That would mean 80 trucks on the road every day! Even if these were electric, the carbon footprint linked to our transportation would be mind-boggling. Let alone the cost.
At full scale, this would look like something like this:
- By truck per day: 28.1 T CO2 per day
- By traditional barge: 12.1 T CO2 per day
- By electric barge: 0 T CO2 per day

We might be prompted to use electric or natural gas trucks as a back-up solution, but if we want to effectively accelerate sustainable mobility, we can’t rely on them as a main transportation means.
Conversely, having a multimodal transportation strategy gives us flexibility – if one mode of transport isn’t available, we can use another one -, it is cost effective – each means of transport is being exploited to its maximum -, and it is better for the planet!